Professional Mold Remediation eliminates the harmful effects of mold by removing, cleaning, and sanitizing affected areas. It also ensures that the problem won’t recur by lowering humidity levels in the area.
The first step is a thorough inspection and assessment. This helps determine the best remediation strategy. Containment is then implemented to prevent mold spores from spreading to other parts of the building. Visit https://utahmoldremovalandremediation.com to learn more.
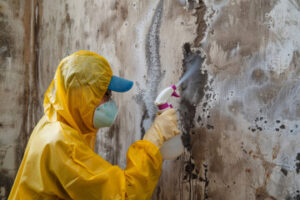
1. Inspection
Mold Remediation specialists inspect homes to identify and address issues that lead to mold growth. Unlike DIY mold removal, this approach addresses the underlying moisture issue so that mold does not return.
During the inspection process, the inspector may use tools like infrared cameras and moisture meters to locate areas of excess moisture in your home. This helps the remediation specialist to understand the extent of your mold problem and create a plan to deal with it.
Infrared cameras and moisture meters can also help the remediation specialist to locate hidden areas of mold growth that are not easily visible to the naked eye. These hidden areas of mold growth are often found in crawl spaces, attics and pipe chases of older homes. It is important to check for these areas of mold as they can be a source of poor air quality and leaks in your building.
If the area of your home where the mold is located is occupied, it is recommended that you notify the occupants about the inspection for their own safety and the health of others. They should be asked to remove items that could block access to the contaminated areas such as furniture or clutter. The occupants of the home should also wear disposable masks and gloves to avoid direct contact with mold.
Once the inspection is complete, the next step is to contain and isolate the affected area. This is usually done by creating an airlock using double layers of polyethylene sheeting and fans to create negative air pressure. This will prevent the movement of mold spores from the clean to the contaminated areas during the remediation process.
2. Containment
When mold is disturbed through cleaning or other work activities, spores are released into the air and can spread to unaffected areas. Proper containment helps to reduce this and protects building occupants.
In addition to sealing off the affected area, other methods of containment can include negative air pressure systems and a misting system to control dust. All workers should use personal protection equipment, including a face mask and goggles. Any vacuum or aspirator used should have a HEPA filter and the exhaust directed to a fume hood or outdoors to minimize spreading the mold spores.
All individuals should be evacuated from the work area if they are unable to safely remain on site during remediation. This includes those with respiratory conditions and weakened immune systems who may be more susceptible to the adverse health effects associated with mold exposure. This should be done with the assistance of trained environmental health professionals, who can ensure that all procedures are followed and that evacuation standards are met.
It is also a good idea to limit the amount of time spent at home during the remediation process, especially if there are significant amounts of widespread mold growth or if you have other medical issues that make it difficult to avoid contaminated materials and surfaces. It is possible to temporarily relocate, such as staying with friends or family, or rent a hotel room during the remediation.
Using moisture permeable materials (such as Tyvek) to cover any collections material that is wet or contaminated will prevent the spread of mold spores during the remediation process. It is a good idea to place contaminated materials that can be discarded in impermeable plastic bags prior to disposal, and to label them before they are placed in the bag. UV radiation/sunlight exposure, used with extreme caution, can also be effective in inactivating small blooms of mold and aiding drying.
3. Removal
When talking with your remediation expert, it is important to be clear on what processes will be used during the mold removal. Different methods are available and your contractor may choose specific procedures based on the size of the affected area, the type of contaminated materials, the cost of removal, and other factors.
In general, a basic mold removal procedure involves cleaning and disinfecting surfaces to kill mold spores. However, this approach is limited because it does not address the underlying issue of moisture and cannot prevent mold from returning if moisture is not properly controlled.
During the cleanup process, the contractor will likely seal off the work area to prevent the spread of mold spores into unaffected areas of your home. This may include using plastic sheeting to block off the work area and tape to seal doors, vents, and windows. A HEPA vacuum cleaner may also be used to clean the surfaces and remove dust particles.
The next step is removing contaminated building materials. This could be as simple as removing drywall in the affected area, or it might require more extensive measures like using blasting equipment to remove moldy plaster and mortar from concrete walls. The type of material removed and how it is removed will affect the amount of airborne spores produced during the process.
If you are unsure whether you or your family will be in the affected area during the remediation process, it is recommended that you vacate the property and seek alternative accommodations. This is especially true if anyone in your household has a respiratory condition or is immunocompromised, as exposure to mold may make these conditions worse.
4. Cleaning
The remediation process will involve a number of steps including assessing, inspecting, and containment. This will allow the professional to determine if your home’s affected materials like drywall, insulation, and flooring can be safely removed. Once all contaminated materials have been removed, the area will be cleaned and disinfected with specialized cleaning agents. This will also involve removing and disposing of any items that have been contaminated by mold. This can include a wide range of items from furniture to rugs. The mold remediation process may also include utilizing air filtration equipment to clean the air in the affected areas and to help prevent spores from spreading.
Depending on the type of mold and the amount of it present, it may be necessary to seal the contaminated surfaces with an anti-microbial solution. This will help to insure that the mold doesn’t return. Moisture control is another important step that will include identifying and fixing the source of moisture in the area. This could include addressing leaks or condensation, and installing dehumidifiers in basements or bathrooms.
It’s important to note that even after the mold is successfully cleaned and remediated, it may still return if the underlying issues have not been resolved. Mold is a symptom of an ongoing moisture problem, and it’s essential that the cause of the mold is addressed in order to avoid future mold growth. Taking action quickly can save you a lot of money and stress in the long run. For this reason, it’s a good idea to contact an experienced mold remediation company to handle the process. This will give you peace of mind that your home is safe for habitation again.
5. Restoration
Once all mold spores have been removed and the affected materials have been cleaned, restoration can begin. This includes repairing or replacing damaged areas and sanitizing the area to ensure that any remaining mold spores can’t regrow. The goal is to restore the property to its pre-mold condition, and this may include recarpeting or repainting.
During this part of the process, it is important to protect yourself and others by wearing protective clothing or disposable coveralls. This helps prevent the spread of spores to unaffected areas, and it is also recommended that you use negative pressure to create an airlock in order to limit the amount of airborne spores.
Affected surfaces and materials are then cleaned or if necessary, they’re removed entirely and safely discarded. During this stage, the professionals will usually use antimicrobial cleaners to penetrate and kill any remaining mold spores. This will often be followed by scrubbing with brushes of different sizes, and in more severe cases, sanding or dry ice blasting is used.
In addition to removing visible mold growth, effective remediation should also address the underlying moisture issues that led to the mold growth in the first place. Otherwise, mold will continue to re-grow and can cause serious health issues and structural damage. For this reason, it’s essential to rely on experienced professionals for any mold remediation or restoration work. If you have any questions, be sure to contact your local housing rights groups who can advise you of your options for legal action against a landlord who refuses to take appropriate action to protect their tenants from harmful mold. They can offer free resources to guide you through the process and help you fight for your rights.